Product Development Stages:
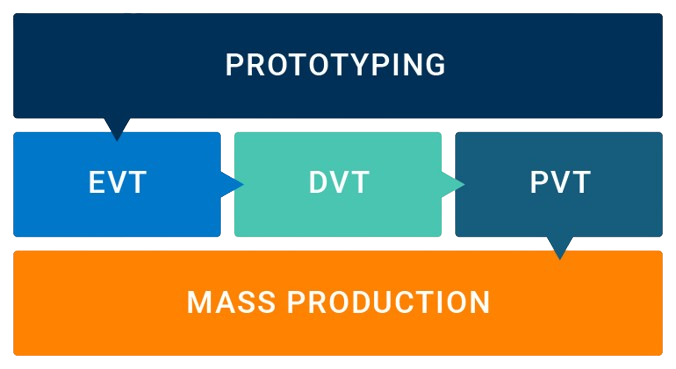
Prototyping:
Prototyping is a crucial stage in the product development process where a preliminary version or prototype of a product is created to validate concepts, test functionality, gather feedback, and make iterative improvements before finalizing the design for mass production. Prototyping is an essential part of the product development lifecycle, enabling innovation, validation, and refinement of ideas to create successful products that meet user needs and market demands.
Engineering Validation Test (EVT):
- EVT is the initial phase of product development where prototypes or early versions of the product are tested extensively.
- The main goal of EVT is to validate the design and functionality of the product and identify any design flaws, issues, or shortcomings that need to be addressed.
- During EVT, engineers perform rigorous testing and analysis to assess the performance, reliability, and compatibility of the product components and subsystems.
- EVT helps in identifying design changes, improvements, or optimizations required to meet the product specifications and requirements.
Design Validation Test (DVT):
- DVT is the stage where the product design is finalized, and pre-production prototypes are subjected to comprehensive testing.
- The primary objective of DVT is to validate and verify that the product meets all the specified requirements, standards, and regulations.
- DVT involves testing the product under various operating conditions, environmental factors, and stress levels to ensure its reliability, durability, and performance.
- Testing during DVT includes functional testing, stress testing, reliability testing, interoperability testing, and compliance testing.
- Any issues, defects, or discrepancies identified during DVT are addressed and resolved before proceeding to the next stage.
Production Validation Test (PVT):
- PVT is the final stage of product development before mass production or commercial release.
- The main purpose of PVT is to validate the production process and ensure that the product can be manufactured consistently and reliably at scale.
- During PVT, production-grade materials, tools, and processes are used to manufacture a small batch of units.
- Testing during PVT focuses on validating the manufacturing process, assessing product quality control measures, and verifying that the manufactured units meet the required standards and specifications.
- PVT helps in identifying any manufacturing issues, defects, or inefficiencies that need to be addressed before full-scale production begins.
Mass Production:
Once the product design has been validated through EVT, DVT, and PVT, mass production can commence. Production facilities scale up manufacturing operations to produce large quantities of the product to meet market demand. Quality control measures are implemented throughout the production process to ensure consistent quality and performance of the finished products.

NPI (New Product Introduction):
New Product Introduction (NPI) is a critical process in the product development lifecycle that involves the transition of a new product from the design and development phase to full-scale production and market launch. NPI encompasses a series of activities and tasks aimed at ensuring a smooth and successful transition, optimizing manufacturing processes, and delivering high-quality products to customers. Here’s an overview of the key aspects of NPI:
1. Cross-Functional Collaboration: NPI requires close collaboration and coordination between various departments and stakeholders, including product design and engineering teams, manufacturing and operations teams, supply chain and procurement teams, quality assurance teams, sales and marketing teams, and external partners or suppliers.
2. Design for Manufacturing (DFM): During the NPI process, product designs are reviewed and optimized for manufacturability. DFM principles are applied to simplify assembly processes, minimize production costs, improve product quality, and enhance overall manufacturing efficiency.
3. Prototype and Pilot Production: Prototyping and pilot production runs are conducted to validate the manufacturing processes, assess product quality, and identify any issues or challenges that need to be addressed before full-scale production. This may involve producing small batches of units for testing, validation, and evaluation purposes.
4. Process Validation and Optimization: Manufacturing processes and procedures are validated and optimized to ensure consistency, reliability, and scalability. This includes setting up production lines, establishing quality control measures, training personnel, and implementing standard operating procedures (SOPs) to meet production targets and quality standards.
5. Supply Chain Management: NPI involves managing the supply chain to ensure timely procurement of materials, components, and resources required for production. Close collaboration with suppliers and vendors is essential to secure the necessary components, mitigate supply chain risks, and maintain inventory levels to support production schedules.
6. Quality Assurance and Testing: Quality assurance measures are implemented throughout the NPI process to monitor and control product quality at every stage of production. Testing and inspection protocols are established to detect defects, deviations, and non-conformities, ensuring that products meet specified requirements and regulatory standards.
7. Documentation and Documentation Control: Comprehensive documentation is created and maintained to record product specifications, manufacturing processes, quality standards, and regulatory compliance requirements. Document control procedures are implemented to manage revisions, updates, and approvals of technical documentation and records.
8. Market Launch and Ramp-Up: Once the product has successfully completed the NPI process, it is launched into the market, and production volumes are ramped up to meet customer demand. Sales, marketing, and distribution strategies are executed to promote the new product, generate awareness, and drive customer adoption.
Overall, NPI is a strategic and disciplined approach to bringing new products to market efficiently and effectively, ensuring alignment with customer needs, business objectives, and market dynamics. By following best practices and leveraging cross-functional expertise, organizations can minimize risks, optimize resource utilization, and achieve success in introducing innovative products that meet customer expectations and drive business growth.
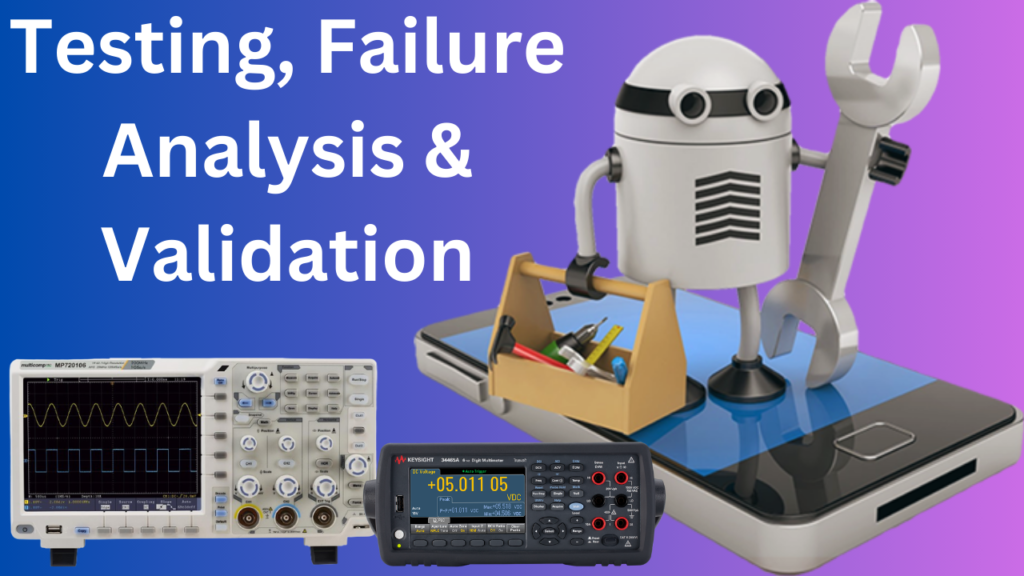
Functional Validation for Mobile Products:
Functional validation for mobile products involves testing each component and feature to ensure that they operate correctly and meet performance specifications. Here’s an overview of functional validation for specific components commonly found in mobile products:
1. Wireless Charger:
– Validate charging functionality: Ensure that the wireless charger can successfully charge the mobile device wirelessly.
– Test charging efficiency: Measure the charging speed and efficiency of the wireless charger under different conditions and with various devices.
– Verify compatibility: Ensure compatibility with different mobile devices and charging standards (e.g., Qi wireless charging).
2. Optical Sensor:
– Validate sensor accuracy: Test the accuracy and reliability of optical sensors, such as ambient light sensors and proximity sensors.
– Verify sensor calibration: Ensure that optical sensors are properly calibrated to detect light levels and proximity accurately.
– Test sensor responsiveness: Validate the responsiveness of optical sensors to changes in ambient light and proximity conditions.
3. Display:
– Validate display functionality: Test the display for brightness, color accuracy, resolution, and viewing angles.
– Verify touch sensitivity: Ensure that the touchscreen display responds accurately to touch inputs and gestures.
– Test display durability: Validate the durability of the display against scratches, impacts, and other physical damage.
4. Battery:
– Validate battery performance: Test battery life, charging speed, and overall performance under different usage scenarios.
– Verify battery health: Monitor battery health metrics such as capacity degradation, charging cycles, and temperature management.
– Test battery safety: Ensure that the battery meets safety standards and regulations to prevent overheating, swelling, or explosion risks.
5. Front Camera (FCAM) and Rear Camera (RCAM):
– Validate camera functionality: Test autofocus, exposure, white balance, image stabilization, and other camera features.
– Verify image quality: Assess image quality in various lighting conditions, resolutions, and shooting modes.
– Test video recording: Validate video recording capabilities, including resolution, frame rate, and audio quality.
6. Motion Sensor:
– Validate motion detection: Test the accuracy and responsiveness of motion sensors, such as accelerometers and gyroscopes.
– Verify orientation detection: Ensure that motion sensors accurately detect device orientation and motion gestures.
– Test gaming and AR functionality: Validate motion sensors for gaming and augmented reality applications, including motion tracking and gesture recognition.
Functional validation for mobile products involves a combination of automated testing, manual testing, and real-world usage scenarios to ensure that each component and feature performs as intended. By conducting comprehensive functional validation, manufacturers can deliver high-quality mobile products that meet user expectations for performance, reliability, and usability.
Power Integrity & System Integrity Validation:
Mobile product validation involves comprehensive testing and validation procedures to ensure that mobile devices meet performance, reliability, and quality standards. Power integrity and system integrity are critical aspects of mobile product validation. Here’s an overview of how power integrity and system integrity are validated in mobile products:
1. Power Integrity Validation:
– Power Delivery Testing: Mobile devices require stable and reliable power delivery to ensure proper operation. Power integrity validation involves testing the power delivery system, including battery, charging circuits, voltage regulators, and power management ICs, to ensure that the device receives the required power under different usage scenarios.
– Voltage Regulation Testing: Voltage regulation testing verifies the stability and accuracy of voltage levels supplied to various components and subsystems within the mobile device. It ensures that voltage fluctuations, noise, and ripple are within acceptable limits to prevent performance degradation and component damage.
– Battery Performance Testing: Battery performance testing evaluates the capacity, efficiency, and longevity of the battery under various charging and discharging conditions. It assesses factors such as battery life, charging time, energy efficiency, and temperature management to ensure optimal battery performance and user experience.
– Power Consumption Analysis: Power consumption analysis measures the power consumption of individual components, subsystems, and software applications running on the mobile device. It helps identify power-hungry components and optimize power management strategies to extend battery life and improve energy efficiency.
– Thermal Management Testing: Thermal management testing evaluates the thermal performance and heat dissipation capabilities of the mobile device under different operating conditions. It ensures that the device remains within safe temperature limits to prevent overheating, component damage, and user discomfort.
2. System Integrity Validation:
– Hardware Validation: Hardware validation involves testing the functionality, reliability, and interoperability of hardware components and subsystems within the mobile device. It includes functional testing, signal integrity analysis, electromagnetic compatibility (EMC) testing, and environmental testing to ensure that the device operates as intended under real-world conditions.
– Software Validation: Software validation verifies the performance, stability, and security of the operating system (OS) and software applications running on the mobile device. It includes compatibility testing, regression testing, security testing, and vulnerability assessments to identify and address software bugs, glitches, and security vulnerabilities.
– Interoperability Testing: Interoperability testing evaluates the compatibility and interoperability of the mobile device with external devices, networks, and software platforms. It ensures seamless connectivity, data exchange, and communication between the mobile device and other devices or systems.
– User Experience Testing: User experience testing assesses the usability, accessibility, and satisfaction of users interacting with the mobile device. It includes user interface (UI) testing, user feedback analysis, and usability studies to identify usability issues, optimize user interactions, and enhance overall user experience.
By performing rigorous power integrity and system integrity validation, mobile device manufacturers can ensure that their products meet quality standards, regulatory requirements, and customer expectations for performance, reliability, and user experience. These validation processes help identify and address potential issues early in the product development lifecycle, minimizing risks and ensuring the successful launch of mobile products into the market.
Failure Analysis, Debugs and DoEs:
Failure analysis, debugs, and Design of Experiments (DoEs) are crucial processes in product development and quality assurance, especially in the context of manufacturing and troubleshooting. Here’s an overview of each:
1. Failure Analysis:
– Definition: Failure analysis involves investigating and identifying the root causes of failures or defects in products, components, or systems.
– Process: It typically involves a systematic examination of failed or defective parts, materials, processes, or systems to determine the underlying factors contributing to the failure.
– Techniques: Failure analysis may include visual inspection, non-destructive testing (e.g., X-ray inspection, ultrasound), material analysis (e.g., microscopy, spectroscopy), and environmental testing (e.g., thermal cycling, humidity testing).
– Purpose: The goal of failure analysis is to understand why failures occurred, identify areas for improvement, and implement corrective actions to prevent similar failures in the future.
2. Debugs:
– Definition: Debugging is the process of identifying, isolating, and resolving issues, bugs, or errors in software, hardware, or systems.
– Process: It involves troubleshooting and analyzing symptoms, error messages, logs, and other indicators to pinpoint the root cause of the problem.
– Techniques: Debugging techniques vary depending on the nature of the problem but may include code review, logging, unit testing, integration testing, and use of debugging tools and software.
– Purpose: The primary objective of debugging is to identify and fix software defects, system malfunctions, or operational issues to restore normal functionality and performance.
3. Design of Experiments (DoEs):
– Definition: Design of Experiments (DoEs) is a statistical methodology used to plan, conduct, and analyze experiments to understand the relationship between input variables and output responses in a system or process.
– Process: It involves systematically varying input factors or parameters while controlling other variables to observe their effects on the system or process output.
– Techniques: DoEs use statistical tools such as factorial designs, response surface methodologies (RSM), Taguchi methods, and analysis of variance (ANOVA) to optimize processes, improve product performance, and identify critical factors influencing quality and reliability.
– Purpose: The purpose of DoEs is to systematically explore and optimize process parameters, identify key variables affecting product quality or performance, and make informed decisions to improve product design, manufacturing processes, and overall quality.
In summary, failure analysis, debugs, and Design of Experiments (DoEs) are essential tools and methodologies used in product development and quality assurance to identify, diagnose, and resolve issues, defects, or performance limitations in products, processes, or systems. By employing these techniques effectively, organizations can enhance product reliability, quality, and customer satisfaction while optimizing manufacturing processes and minimizing risks.
General Electrical Engineering (EE) Equipment:
Electrical Engineering (EE) Equipment, including oscilloscopes, spectrum analyzers, logic analyzers, power analyzers, probes, digital multimeters (DMMs), and LCR meters, serve various purposes across different domains within electrical engineering. Here’s how each type of equipment is commonly used:
1. Oscilloscope:
– Measures and displays voltage signals over time.
– Used for waveform analysis, time-domain measurements, and signal integrity testing.
– Helps visualize analog and digital signals, measure voltage levels, frequency, amplitude, and phase relationships.
2. Spectrum Analyzer:
– Analyzes frequency spectra of electrical signals.
– Identifies frequency components, harmonics, noise, and interference in signals.
– Essential for RF engineering, telecommunications, audio signal analysis, and frequency-domain measurements.
3. Logic Analyzer:
– Captures, displays, and analyzes digital signals in digital systems.
– Used for debugging, timing analysis, protocol decoding, and troubleshooting digital circuits and embedded systems.
– Helps identify logic errors, timing violations, and signal integrity issues in digital designs.
4. Power Analyzer:
– Measures electrical power parameters such as voltage, current, power factor, and energy consumption.
– Analyzes power quality, efficiency, and distribution in electrical systems.
– Helps optimize power management, improve energy efficiency, and troubleshoot power-related issues.
5. Probes:
– Connects test equipment to the device under test (DUT).
– Enables safe and accurate measurements of voltage, current, and signals.
– Available in various types (e.g., passive probes, active probes, differential probes) for different measurement requirements and signal characteristics.
6. Digital Multimeter (DMM):
– Measures voltage, current, resistance, capacitance, and continuity.
– Performs general-purpose electrical measurements, troubleshooting, and testing.
– Used in electronics, electrical maintenance, and circuit debugging.
7. LCR Meter:
– Measures inductance (L), capacitance (C), and resistance (R) of electronic components.
– Characterizes passive components such as capacitors, inductors, and resistors.
– Used in component testing, quality control, and circuit design to ensure component specifications and performance.
Each type of equipment plays a vital role in electrical engineering tasks such as design, testing, troubleshooting, and validation of electronic circuits, systems, and devices. Electrical engineers rely on these tools to analyze signals, characterize components, verify specifications, and ensure the functionality, performance, and reliability of electrical and electronic systems.
I2C, I2S, SPI, SPMI, UART, and USB Protocols:
The I2C, I2S, SPI, SPMI, UART, and USB—are commonly used in mobile devices for communication between different components, peripherals, and external devices. Here’s how they are utilized for mobile product validation:
1. I2C (Inter-Integrated Circuit):
– Used for communication between integrated circuits, sensors, and other peripherals within the mobile device.
– During validation, engineers ensure that I2C devices communicate correctly, exchange data, and respond to commands as expected.
– Validation may involve testing the integrity of data transmission, addressing schemes, clock synchronization, and protocol compliance.
2. I2S (Inter-IC Sound):
– Used for digital audio communication between components such as audio codecs, digital signal processors (DSPs), and microcontrollers.
– During validation, engineers verify the quality and integrity of audio data transmission, synchronization between audio streams, and compatibility with audio peripherals and codecs.
– Validation may include testing audio playback, recording, sampling rates, bit depth, and audio channel configurations.
3. SPI (Serial Peripheral Interface):
– Used for high-speed synchronous communication between microcontrollers, sensors, displays, memory devices, and other peripherals.
– During validation, engineers ensure proper initialization, data transfer, clock synchronization, and error handling in SPI communication.
– Validation may involve testing SPI device configuration, data integrity, clock frequency, and protocol compliance.
4. SPMI (System Power Management Interface):
– Used for communication between power management ICs (PMICs) and system-on-chip (SoC) components to manage power distribution, voltage regulation, and battery charging.
– During validation, engineers verify proper power sequencing, voltage scaling, current monitoring, and thermal management using the SPMI protocol.
– Validation may include testing power states, voltage transitions, current consumption, and fault detection in power management subsystems.
5. UART (Universal Asynchronous Receiver-Transmitter):
– Used for asynchronous serial communication between microcontrollers, peripherals, and external devices.
– During validation, engineers ensure reliable data transmission, baud rate configuration, start/stop bit synchronization, and error detection in UART communication.
– Validation may involve testing UART device initialization, data framing, flow control, and error handling.
6. USB (Universal Serial Bus):
– Used for high-speed serial communication, data transfer, and power delivery between mobile devices and external peripherals such as USB flash drives, keyboards, mice, and external displays.
– During validation, engineers verify USB device detection, enumeration, data transfer rates, power negotiation, and compliance with USB standards.
– Validation may include testing USB device interoperability, compatibility with USB hosts, power consumption, and error recovery mechanisms.
In mobile product validation, engineers use specialized test equipment, protocol analyzers, simulation tools, and software frameworks to validate the functionality, performance, and interoperability of devices and subsystems using these communication protocols. Validation ensures that mobile products meet quality standards, regulatory requirements, and user expectations for reliability, performance, and compatibility.